- today
- label News
- favorite 0 likes
- remove_red_eye 7861 views
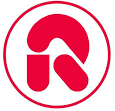
DIESEL FUEL INJECTION: YOUR COMPLETE GUIDE
Since its invention in Germany in 1893 by Rudolf Diesel, the Diesel injection engine has revolutionized the entire sector of vehicles and motorized machinery. The first working version of the Diesel engine was tested in 1897, and over time, it has undergone many significant developments. Nevertheless, Diesel injection remains the key phase in the operation of this type of engine and its fundamental distinguishing feature.
It is around the Diesel injection mechanism that most research and optimization activities have taken place, aiming to develop increasingly innovative and high-performance versions. As a result of this research, it is undoubtedly the injection system that fuels diesel combustion that has changed the most, technically, over the years.
1. HOW DOES A DIESEL ENGINE WORK
Diesel engines operate through spontaneous combustion of the fuel: unlike gasoline, diesel ignites without an external spark due to the high pressure and temperature of the compressed air. The cycle of a Diesel engine follows four phases:
1. Intake: air is drawn in, filtered, and compressed in the cylinder.
2. Compression: the piston compresses the air, increasing its temperature.
3. Combustion: diesel fuel, injected at high pressures, ignites upon contact with the hot air.
4. Exhaust: the produced fumes are expelled from the engine.
This cycle enables efficient combustion and reduces fuel consumption, one of the reasons why Diesel engines are valued for applications requiring high performance and durability.
2. DIFFERENT TYPES OF DIESEL FUEL INJECTION
2.1 DIRECT INJECTION
The direct injection system is now the standard in modern Diesel engines, as it injects fuel directly into the cylinder's combustion chamber, ensuring precision and greater efficiency. This approach offers:
- superior energy efficiency due to more complete combustion;
- optimized engine performance;
- greater control over the amount of fuel injected, reducing emissions and consumption.
Common Rail: the evolution of direct injection
The Common Rail system represents the latest advancement in direct injection technology, based on a common supply system for all injectors. Instead of storing pressure within each injector, the Common Rail uses a high-pressure tube that supplies all injectors simultaneously. This system provides several significant advantages:
- Constant and adjustable pressure: fuel reaches extremely high pressures and is precisely metered;
- Multi-phase injection: enables optimization of each combustion cycle, improving engine responsiveness;
- Noise reduction: gradual fuel delivery reduces noise levels.
2.2 INDirect INJECTION
Indirect injection is a less efficient and now outdated technology, in which diesel fuel is injected into a pre-combustion chamber heated by glow plugs. Although simpler, this system results in less efficient combustion and higher fuel consumption compared to direct injection.
3. THE COMMON RAIL DIESEL SYSTEM: OPERATION AND RELIABILITY
The Common Rail remains the most widely used fuel injection system in Diesel engines. Comprising an injection pump, a rail (a high-pressure common conduit), injectors, and sensors connected to an electronic control unit (ECU), this system enables precise control over the pressure and quantity of fuel injected. The pump pressurizes the fuel and sends it to the rail, which acts as an accumulator, maintaining a constant pressure that is electronically regulated. The injectors, positioned along the rail, receive the fuel and, under ECU control, inject it into the combustion chamber with maximum precision using electromagnetic or piezoelectric valves. This process allows for multiple, closely timed injections that enhance combustion and optimize engine efficiency. Additionally, thanks to a modular design, the Common Rail system can easily adapt to modern vehicle engines, delivering smooth and powerful performance.
4. ADVANTAGES OF common rail DIESEL INJECTION
The Common Rail system offers several significant advantages over traditional injection systems, making Diesel engines an increasingly attractive choice in terms of performance and sustainability. Here are the main advantages of the Common Rail engine:
a) High fuel pressure: the system maintains optimal pressure to ensure efficient combustion.
b) Precision in delivery: thanks to electronic control technology, the injectors can meter fuel with extreme accuracy, impacting power, consumption, and emissions.
c) Reduced emissions: precise metering and optimized combustion lower the production of polluting gases.
d) Increased power and reduced noise: progressive and controlled injection reduces noise, improving vehicle comfort.
5. COMMON RAIL DIESEL INJECTORS: MODELS AND FEATURES
Injectors are essential components in the Common Rail system, as they determine the quantity and speed of fuel delivered into the cylinder. There are two different types of Diesel injectors, each with unique structural characteristics, suitable for various applications and vehicle types.
5.1 SOLENOID DIESEL INJECTORS
Solenoid injectors regulate fuel injection through a control valve that opens and closes using magnetic force, utilizing a solenoid positioned on the actuator.
5.2 PIEZOELECTRIC DIESEL INJECTORS
Piezoelectric injectors offer greater responsiveness compared to solenoid types, as they use piezoelectric elements that function by converting applied voltage changes into expansion and contraction actions (i.e., movement). A distinctive feature of these injectors is the incorporated piezoelectric stack that contains all piezoelectric elements.
6. MAINTENANCE AND CLEANING OF DIESEL INJECTORS
Maintaining Diesel injectors is essential to ensure optimal performance and prolong engine life. Over time, impurities accumulate in all fuels, which can cause malfunctions or compromise injector performance and vehicle fuel efficiency. So, how can you tell when it’s time to clean the injectors?
Main signs of a clogged injector
It’s important to recognize the symptoms that indicate when injector cleaning is needed. Here are some signs that it’s time to maintain the injectors:
- Difficulty starting the engine
- Increased fuel consumption
- Reduced performance
- Black smoke emissions from the exhaust
7. THE IMPORTANCE OF REGULAR AND PROFESSIONAL MAINTENANCE
Regular maintenance of injectors, using appropriate cleaning tools and specific additives, can help prevent the issues mentioned above, preserving the injection system. Conducting periodic, thorough inspections is essential, along with following some best practices:
a. Regular cleaning: using quality additives helps prevent deposits in the injectors.
b. Pressure check: ensuring the fuel pressure is correct to avoid malfunctions.
c. Seal replacement: components such as seals and spacers should be checked and replaced if worn.
Diesel injector maintenance should not be underestimated, and professional servicing can be the key to ensuring many more years of useful life and high performance for your Diesel engine.
8. QUALITY SPARE PARTS FOR DIESEL INJECTORS OF LEADING BRANDS
Injector maintenance sometimes goes beyond mere cleaning: there comes a time when it's necessary to replace injector components due to wear or damage, making it essential to have a reliable source for high-quality spare parts.
REDAT specializes in supplying spare parts for Diesel injectors, ideal for ensuring proper injection system functionality. Key available parts include:
- Injector repair kits: containing the parts needed for injector refurbishment.
- Seals and shims: essential components for maintaining optimal pressure levels.
- Remanufactured injectors: a cost-effective and sustainable solution.
Choosing quality spare parts is crucial for preserving Diesel engine efficiency and reducing long-term costs.
9. REDAT, YOUR TOP PARTNER TO GIVE NEW LIFE TO YOUR DIESEL ENGINE
REDAT is the ideal partner for those seeking quality spare parts, tools, and repair kits for Common Rail Diesel injectors from the industry's top brands. We ensure an excellent quality-to-price ratio and guarantee outstanding results in component performance and the fully refurbished injector with our products.
With decades of experience in manufacturing spare parts for injectors, injection pumps, refurbished injectors, and Diesel injector repair tools, we fulfill customer needs by providing quality comparable to original parts.
Our products cover most injection systems available on the market across all sectors—Automotive, Industrial, Marine, and Agricultural—and in our aftermarket catalogs, you will find spare parts for leading brands: Caterpillar-Perkins, Denso, Bosch, Delphi, L’Orange-MTU, Cummins, Unit Injector, Siemens.
Visit our website to learn more about our range of spare parts and contact us for any inquiries.
WWW.REDAT.US
Redat North America
120 Bonnie Loch Ct
Orlando, Florida 32806
United States
U.S.A. +1 (800) 327-2017
International +1 407-246-1600
sales@redatnorthamerica.com